ITPS
RetrospectivePromecam Model RG Hydraulic Press Brake Manual Plastic Comb – January 1, 2010 by Promecam (Author) See all formats and editions Hide other formats and editions. Amada promecam hydraulic press brake manual at greenbookee.org - Download free pdf files,ebooks and documents of amada promecam hydraulic press brake manual. Amadas New AC-NT Series Servo Drive Turret and Reduced Operating Tuesday, June 06 15 / pdf. Amada is known worldwide as the leader in turret punch press. Program the Press Brake.
Tools are always aligned and parallel
Good bending accuracy depends on perfect tool alignment, what ever the position oft he beams.
The first priority is tooling alignment in itself. All punches and dies have their axes at a pre-determined distance from the location face. Therefore, once the tools are fitted they are automatically aligned.
The second priority is alignment during the bending operation. For this reason, the lower beam is guided by a large number of precision bearings spaced out over the whole length of the beam. These bearings are greased for life. They require no maintenance and do not wear, guiding remains accurate for the whole life of the press.
Safety is of prime importance
Present in all major industrial countries throughout the world, for many years, AMADA has complied with the specific safety requirement of each market with regard to the design of the machine. By following the legislation in force in Scandinavia, AMADA PROMECAM has already satisfied the most demanding regulations in the world.
Adjustable distance pieces
Residual differences of penetration can be further reduced by adjustable distance pieces, which allow ultimate bending precision. Besides this, they protect the beams against local overloading and are sufficiently spaced to facilitate the manufacture of boxes. Their design is such that the punch can be mounted both. sides, allowing easier execution of specific shapes.
Rapid tool clamping
AMADA PROMECAM has developed two methods which give instantaneous clamping of all available top tools. both systems prevent the long manual operation usually associated with a tool change, thus considerably reducing lost time due to tool change. The hydraulic equipment also prevents any risk of the tools falling down, thanks to the design of the clamp section. Manual locking is achieved very quickly by the use of a single lever on each clamp.
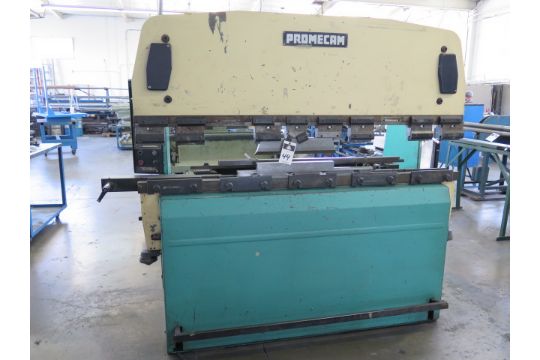
Precision
The quality of a bend lies in the accuracy of the angle throughout the whole of its length. The precision is directly related to the punch penetration into the die, the smallest variation leads to serious discrepancies in the angle of bend.
The real problem - all presses deflect
Traditional presses have a lower beam which is integral with the frame. 6.5 turbo diesel engine torque specs. The upper beam is the moving member and is controlled by two cylinders : under bending load, the resultant reaction leads to opposite deflection of the beams, which gives angle variation over the entire length of the bend.lowerbeam which is integral with the frame. Theupper beam is the moving member and iscontrolled by two cylinders : under bending load,the resultant reaction leads to opposite deflectionof the beams, which gives angle variationover the entire length of the bend.
In order to reduce this effect, beams are crowned and frames are often oversized within the limits of space available and cost.
AMADA PROMECAM has succeeded in cancelling out the effects of deflection : by using centralthrust. On a PROMECAM ITS or ITPS Pressbrake, the lower beam does the work, through the action of cylinders placed centrally in the lower beam. During the bending operation both beams deflect in the same direction, therefore the bend is constant over the whole length of the piece. For downstroking Press brakes, AMADA PROMECAM has retained the principle of constant parallelism, by using a composite beam, which has been patented in 20 countries.
The mastery of deflection is of greater consequence to precision bending, as without it, electronic and hydraulic monitoring on press brakes cannot be claimed as being effective.
Attemps to overcome the problem: time and money lost
In an attempt to reduce the effects of deflection, operators are tempted to introduce estimated shim values under punches or dies.
This sort of accuracy, which is obtained by a hitor-miss method, is hazardous, and the time spent increases the cost of the product.
Manufacturers have arrived at several solutions such as a machined lower beam, or mechanically / hydraulically adjustable crowning devices placed under the dies.
These systems are costly, always complex, often unreliable, and require long, delicate, and usually unsatisfactory adjustment.
- Adjustment of compensation pressure
- Adjustable crowning presse before bending but at fixed value during bending
Chart for air-bending
This chart is based on 40/45 daN/mm2 tensile strength steel. Being generally aware of two factors, sheet thickness e and inner radius of the bend ri, it is possible to read directly from the chart:
- The tonnage in tons per metre of the lengthto be bent F.
- The dimension of the smallest flange possible b.
- The opening of the die to be used V.
The advised die openings are givenin the dark squares. The V opening is related to the thickness e of the sheet to be bent. The advised values are the following:
For e ≤ 10 mm Vee die 8 e
For e ≥ 12 mm Vee die 10 e Standard horizon hx300 manual.
If the advised opening cannot be used (unacceptable flange, tooling unavailable, or insufficient tonnage), select a die shown in the adjacent light-coloured squares of the chart.
To bend other materials (stainlesssteel, aluminium .. ) this chart remains valid. It is only necessary to correct the ratio of the tensile strength.
For example, if this chart, based on 40/45 daN/mm2 steel shows a tonnage of 500 kN for a given bend, the tonnage will be of 250 kN for 20 daN/mm2 aluminium sheet.
Our current products
Fast & Accurate, Ergonomic & Compact
Promecam Press Brake Parts

Precision
The quality of a bend lies in the accuracy of the angle throughout the whole of its length. The precision is directly related to the punch penetration into the die, the smallest variation leads to serious discrepancies in the angle of bend.
The real problem - all presses deflect
Traditional presses have a lower beam which is integral with the frame. 6.5 turbo diesel engine torque specs. The upper beam is the moving member and is controlled by two cylinders : under bending load, the resultant reaction leads to opposite deflection of the beams, which gives angle variation over the entire length of the bend.lowerbeam which is integral with the frame. Theupper beam is the moving member and iscontrolled by two cylinders : under bending load,the resultant reaction leads to opposite deflectionof the beams, which gives angle variationover the entire length of the bend.
In order to reduce this effect, beams are crowned and frames are often oversized within the limits of space available and cost.
AMADA PROMECAM has succeeded in cancelling out the effects of deflection : by using centralthrust. On a PROMECAM ITS or ITPS Pressbrake, the lower beam does the work, through the action of cylinders placed centrally in the lower beam. During the bending operation both beams deflect in the same direction, therefore the bend is constant over the whole length of the piece. For downstroking Press brakes, AMADA PROMECAM has retained the principle of constant parallelism, by using a composite beam, which has been patented in 20 countries.
The mastery of deflection is of greater consequence to precision bending, as without it, electronic and hydraulic monitoring on press brakes cannot be claimed as being effective.
Attemps to overcome the problem: time and money lost
In an attempt to reduce the effects of deflection, operators are tempted to introduce estimated shim values under punches or dies.
This sort of accuracy, which is obtained by a hitor-miss method, is hazardous, and the time spent increases the cost of the product.
Manufacturers have arrived at several solutions such as a machined lower beam, or mechanically / hydraulically adjustable crowning devices placed under the dies.
These systems are costly, always complex, often unreliable, and require long, delicate, and usually unsatisfactory adjustment.
- Adjustment of compensation pressure
- Adjustable crowning presse before bending but at fixed value during bending
Chart for air-bending
This chart is based on 40/45 daN/mm2 tensile strength steel. Being generally aware of two factors, sheet thickness e and inner radius of the bend ri, it is possible to read directly from the chart:
- The tonnage in tons per metre of the lengthto be bent F.
- The dimension of the smallest flange possible b.
- The opening of the die to be used V.
The advised die openings are givenin the dark squares. The V opening is related to the thickness e of the sheet to be bent. The advised values are the following:
For e ≤ 10 mm Vee die 8 e
For e ≥ 12 mm Vee die 10 e Standard horizon hx300 manual.
If the advised opening cannot be used (unacceptable flange, tooling unavailable, or insufficient tonnage), select a die shown in the adjacent light-coloured squares of the chart.
To bend other materials (stainlesssteel, aluminium .. ) this chart remains valid. It is only necessary to correct the ratio of the tensile strength.
For example, if this chart, based on 40/45 daN/mm2 steel shows a tonnage of 500 kN for a given bend, the tonnage will be of 250 kN for 20 daN/mm2 aluminium sheet.
Our current products
Fast & Accurate, Ergonomic & Compact
Promecam Press Brake Parts
Promecam Press Brake Manual Diagram
Promecam Press Brake Manual Pdf
|